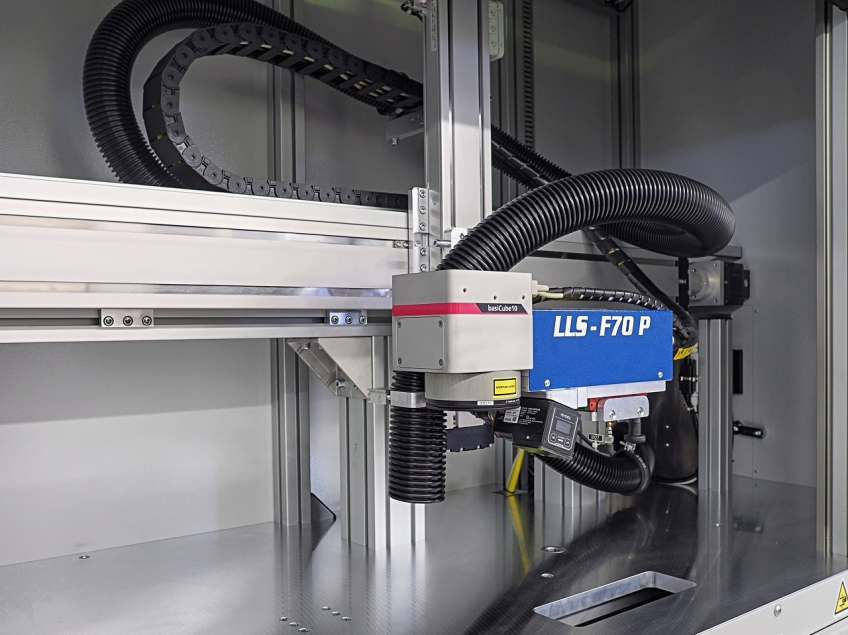
How to choose the right laser for your application?
Choosing the right laser for a particular application depends on several key factors that must be considered to ensure the laser meets specific requirements. Our first question when meeting with a customer is what material the laser will process. Knowledge of the material is crucial to determine the appropriate laser wavelength that will be well absorbed in the material. This means that the energy that the laser delivers to the material will be used efficiently for processing, whether it is laser cutting, laser marking or laser welding.
Laser welding of plastics Laser marking Laser drilling
For the processing of metallic materials, we predominantly use fibre or crystal lasers. The fibre lasers we supply have a wavelength of 1064 nm (near-infrared radiation) and are suitable for processing most metallic materials and some plastics. We also supply laser sources with second and third harmonic frequencies, i.e. wavelengths derived from the fundamental wavelength of 1064 nm, namely green laser (532 nm) and UV laser (343 nm). These lasers are also suitable for the processing of metallic materials, but in particular for the processing of various types of plastics, ceramics and glass. These lasers also find their application in miniaturization, due to the fact that shorter wavelengths can be more focused and thus achieve a smaller laser spot diameter than a conventional fibre laser. We use CO2 lasers with a wavelength of 10600 nm to process non-metallic materials and organic materials (leather, wood...).
Once the laser wavelength is determined, a suitable laser source power is then selected to ensure that the quality, tact and price match the customer's expectations. The most common laser source we supply is a fibre laser with an average power of 20 W. This is a source suitable for common marking or cutting thin sheets. As the need for fast marking increases, so does the need for an increase in power to maintain the amount of energy required to affect the material. For very fast marking of aluminium alloys, for example, we supply 70 W lasers, and for engraving we also supply 100 W fibre lasers. Our portfolio includes air-cooled fibre lasers up to 600 W average power, which are suitable for perforation or cleaning, for example, with very high process efficiency.
Laser cleaning using 100W and 300W laser source
For the processing of non-metallic materials, we supply CO2 lasers in the power range from 10 to 150 W, covering the entire range of applications from marking to cutting several millimetres wide plastics.
We also use fibre lasers for welding plastics and metals, but they differ in their power and beam quality. We have these in power outputs of typically 200 and 300 W for welding plastics and thin sheet metal, but we can also supply high power lasers with power outputs of units of kW, which can provide a penetration of several millimetres.
If, on the other hand, there is a high demand for processing quality, e.g. products for the medical sector, another parameter to be monitored is the pulse length. Our commonly supplied fibre lasers operate with pulses in units of up to hundreds of nanoseconds, green lasers with pulses of units of nanoseconds and CO2 lasers operating in continuous mode. For very precise micromachining, on the other hand, laser sources operating with pulse lengths in the order of femtoseconds to picoseconds are preferably used. With such short pulses, the principle of interaction of the laser beam with the material is changed and there is much less thermal effect on the material. For example, no burrs or other thermally affected areas are created. The disadvantage of these lasers is still their price, which is higher compared to conventional nanosecond fibre lasers.
And why a laser from us? Lintech, spol. s.r.o. purchases laser sources from the largest laser manufacturers on the market. Their advantage is very long lifetime, quality and stability of the laser radiation. We then select other components for the laser sources and assemble our own OEM assemblies, which we put into our machines or provide to the customer for their own integration into the machine or production line.
LINTECH has its own application laboratory where all the above mentioned laser sources are located. We will test on your samples and recommend the most suitable laser for your application.